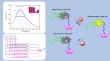
Overview
Discover Nano is an open access journal publishing research from across all areas of nanoscience and nanotechnology.
- Indexed in SCIE; published papers will be listed in Web of Science.
- Formerly Nanoscale Research Letters (6.5 2022 Impact Factor), Discover Nano will receive its first Impact Factor under the new name in 2025.
- Covers nanoscale research in physics, materials science, biology, chemistry, engineering.
- A Discover journal focused on speed of submission and review, service, and integrity.
- Editor-in-Chief
-
- Jiang Wu,
- Yu-Lun Chueh
- Submission to first decision (median)
- 13 days
- Downloads
- 2,128,888 (2023)
Latest articles
Journal updates
-
Become an Editorial Board Member
We are recruiting new Editorial Board Members.
-
Meet the Editors-in-Chief for Discover Nano
Learn more about our Editors-in-Chief
-
Writing your manuscript: interactive author tutorials
Looking to publish in a Discover journal? Springer Nature provides interactive tutorials to help you as an author write the best article possible by providing points to consider, from your background reading and study design to manuscript structuring and figure preparation. Find out more.
-
Introducing In Review
In Review, a new preprint service brought to you by Research Square, is available on Discover Nano. By opting in to this service, you will be able to:
- Showcase your work to funders and others with a citable preprint while it is under review
- Track the status of your manuscript through the peer review process on a more granular level
- Benefit from early sharing, such as more collaboration opportunities and earlier citations.
See the full range of benefits of In Review and how to opt-in
Journal information
- Electronic ISSN
- 2731-9229
- Abstracted and indexed in
-
- AGRICOLA
- ANVUR
- Astrophysics Data System (ADS)
- BFI List
- Baidu
- CLOCKSS
- CNKI
- CNPIEC
- Chemical Abstracts Service (CAS)
- Chinese Academy of Sciences (CAS) - GoOA
- Current Contents/Physical, Chemical and Earth Sciences
- DOAJ
- Dimensions
- EBSCO
- EI Compendex
- EMBiology
- Google Scholar
- Naver
- OCLC WorldCat Discovery Service
- Portico
- ProQuest
- PubMedCentral
- SCImago
- SCOPUS
- Science Citation Index Expanded (SCIE)
- Semantic Scholar
- TD Net Discovery Service
- UGC-CARE List (India)
- Wanfang
- Copyright information
-
© Springer Science+Business Media, LLC, part of Springer Nature